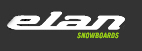
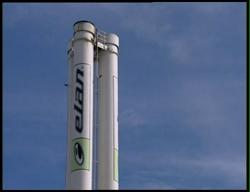
Als der Krieg vorbei war gab es diese kleine Werkstatt immer noch und die Urmutter einer der weltweit größten Wintersportartikelhersteller hatte sich über seine Notwendigkeit hin bewährt.



Angefangen beim Verkleben der einzelnen Lagen (Base, Holzkern, Glasfasern, Seitenwangen, Kanten) in der Presse. Wusstet ihr eigentlich wie viel Leim in einem Brett eigentlich drinnen steckt?!? Ich kann euch sagen… es ist ein Haufen! Nachdem das Brett bis zu 18 Min. in der Presse war, geht es weiter zu einem Kerl, der in sekundenschnelle die überstehenden Ränder von Hand absägt. (Man hat mir gesagt, dass sie diesen Herren durch einen Roboter ersetzten wollten… bis heute haben sie aber noch keinen gefunden, der schneller uns sauberer arbeitet!)
Nach dem Aussägen geht es weiter zum ersten Kantenschliff. Auch erstmal von Hand versteht sich.

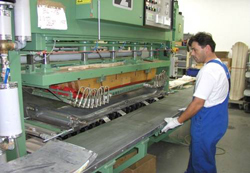
Dann geht das Brett auf eine lange Reise durch viele, lustig blinkende Maschinen und Apparate.
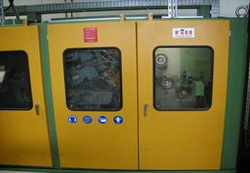

Maschinelles Schleifen, Base säubern, 1. Quality Control, erneuter Kantenschliff mit einer Maschiene, die mit Diamanten schleift, wachsen, waschen, föhnen, legen… Handschliff der Base, 2. Quality Control unter Röntgen, nachschleifen des Topsheets, Topsheet-Lasur, Politur…(es befinden sich noch zahlreiche Schritte dazwischen, die aber den Umfang dieses Berichtes sprengen würden). Am Ende der Produktion warten noch verschiedene Belastungstests auf das Brett, um dem Käufer auch die gewünschte Qualität zu garantieren.

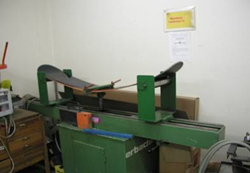
Insgesamt dauert der Produktionsprozess, je nach Boardtyp, bis zu zwei
Stunden. Neben der Sandwichproduktion produziert Elan auch noch
aufgeschäumte Bretter, um denen von uns, die es nicht so dicke haben,
den Spaß im Schnee nicht zu verwehren. Elan setzt sehr viel daran,
überall, wo es möglich ist, Gewicht einzusparen. Das dreilagige DG 70
Fiberglass spart 300 Gramm gegenüber herkömmlichen Fiberglass ein. Das
DG Top Printing spart insgesamt 12% an Gewicht gegenüber Brettern
anderer Marken ein und ist deswegen nicht umsonst patentiert und somit
einzigartig. Es lebe der technische Fortschritt!


Wer Lust hat, kann sich in diesem Betrieb auch sein eigenes Snowboard
graphisch gestalten lassen! Ja, ja, kein Scherz! Ihr müsst nicht Herr
Nitro in Person sein und eine Auflage von 1000 Brettern bestellen, um
euern individuellen Style auf eines der freshen Artec-Boards von Elan
zu bekommen. Je nach Umfang der Grafik wird hier zwischen Siebdruck
(für die etwas filigraneren Zeichnungen) und dem patentierten
Laserdruck (Blueprint) entschieden. Wer sich stylemäßig abheben will
und das nötige Kleingeld hat, checkt am besten mal www.artecproject.com/blueprint/en/ aus.

Übrigens: Eine Große Auswahl an Brettern von Elan findet Ihr auch in unserem Shop. Schaut einfach mal im Boardshop vorbei, oder checkt die Webseite!
www.boardshop.de
www.elansnowboards.com
Fabian Karg aka. Fabson
Produkte, die Dich interessieren könnten
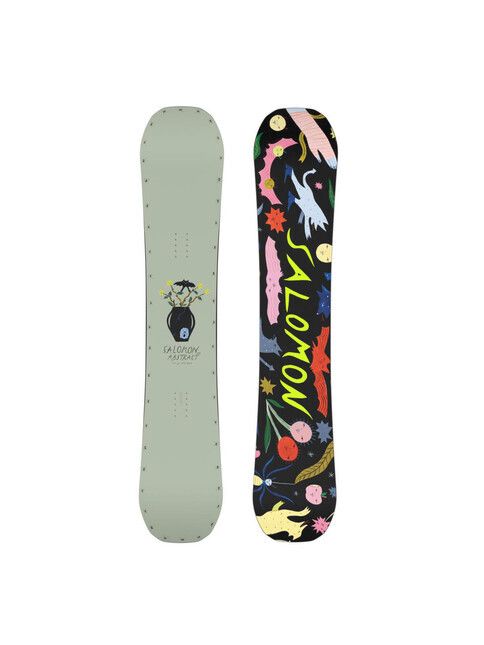
Snowboard Abstract wide 24/25
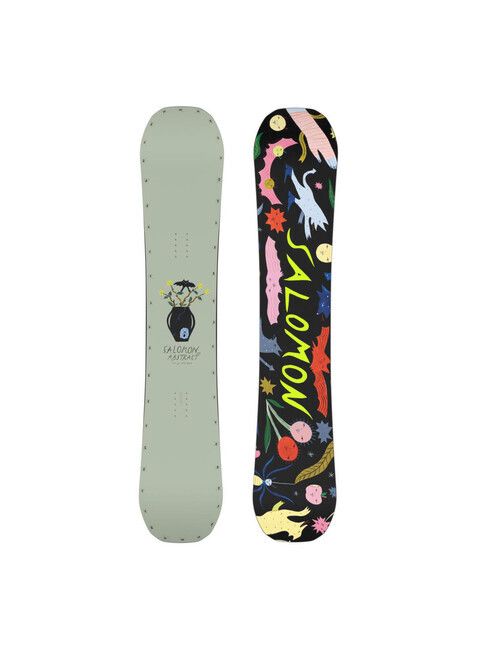